はじめに
従来の電池に比べ優れた安全性、長寿命といった特長を有し、注目が集まる全固体電池は、早期実用化が期待されています。今回は全固体電池の特徴と当社の機器をご紹介いたします。
全固体電池とは
全固体電池とは、その名前の通り電池を構成するすべての部材が「固体」である電池のことです。従来の二次電池は、電解質に液体が使われていますが、全固体電池は電解質として固体(無機固体電解質)を用います。電解質はイオンが内部で動き回り、電極に十分な電気を流せる材質を使用します。
全固体電池のメリット
温度変化に強い
有機化合物を含む電解液は、低温で粘度が高くなることから内部抵抗が上昇し、電圧が低下します。逆に高温では液漏れ・発火の危険性があり安全性への懸念があります。そのため、現在使用されているリチウムイオン電池(LIB)は、ある一定の温度範囲での電池使用が推奨されています。一方、全固体電池で使用する固体電解質は温度による物質の変化がないため、安定性が高く、温度変化の影響を受けにくいことが特長です。この温度変化への強さは、応用先と期待される電気自動車(EV)に搭載するにあたり大きなメリットがあります。現在、EVに積むLIBでは高温に備えて冷却装置を取り付けていますが、全固体電池はその必要がなく、そのスペースを活かしより多くの電池を搭載できることから走行距離が伸びることが期待されています。
急速充電が可能
通常、急速充電を行う場合は、通常よりも大きな電流を流すため電池が発熱し高温になります。電池は高温になるほど化学反応は進行しやすく充電が進みますが、リチウムイオン電池の場合、電池として本来起こるべき反応以外の副反応も促進し劣化してしまいます。つまり、リチウムイオン電池の急速充電には限界があります。一方、全固体電池は上記にあるように急速充電による熱の影響を受けません。そのため、小型の電池を多層化することで容量を高めることができます。全固体電池の充電時間はリチウムイオン電池の3分の1の時間であると言われ、EVのように急速充電が求められる用途に適しています。
全固体電池の課題
現在、固体電解質は大きく分けて硫化物系と酸化物系の2種類があります。
硫化物系固体電解質の製造の課題
硫化物系の固体電解質は電解液と同等のイオン伝導度を持ち、エネルギー密度の高い全固体電池となります。しかし、硫化物系の課題として挙げられるのが製造時の水分除去です。硫化物系は大気中の水分と反応し有毒ガス(硫化水素)を発生します。安全性を保ち製造するには、ドライルームやプロセス内の水分を除去した環境(クローズドシステム)での製造が必須となります。
酸化物系固体電解質の製造の課題
全固体電池は、複合正極層/隔離層/複合負極層の3層から成っており、リチウムイオンが正・負極内および隔離層内の固体電解質粒子を介して複合正・負極間を移動することで充放電をします。リチウムイオンは粒子接点を介して移動するため、粒子間接触はエネルギー密度に大きく影響します。硫化物系固体電解質に比べ一般的な酸化物系固体電解質粒子は硬く粉砕に大きなエネルギーを必要とします。しかし、粉砕により結晶構造が破壊されると特性が大幅に低下します。これを解消するためには結晶構造を破壊せず粉砕すること、または、微粒化した固体電解質と活物質粒子を複合化することが必要であると言われています。
最近の研究では、「高容量電極活物質であるLi2SとSiは従来材料であるLiNi1/3Co1/3Mn1/3O2やグラファイト等の層状化合物と異なり、結晶構造が壊れても充放電特性の低下がないことから、遊星ボールミルを用いたメカニカルミリングで微細化することで電池特性を向上できることが知られている。また、一般的な硬い酸化物系固体電解質材料をメカニカルミリングにより合成される高変形性酸化物系固体電解質材料に置き換えることで粒子間接点を大幅に増やすことができる¹⁾ 」ということが分かっており、電極活物質と導電材をメカニカルミリングにより電極内固体電解質の材料合成と複合化を同時に行う研究も進んでいます。
メカニカルミリングについて
メカニカルミリング (Mechanical Milling: MM)法とは、金属素粉末や合金粉末にアトライタやボールミルを用いてミリング(強撹拌)し、粉末に対して超強加工を施すことができる方法です²⁾。メカニカルアロイング( Mechanical alloying )やメカニカルグライディング(Mechanical grinding)はメカニカルミリングの一種です。メカニカルアロイングは異種金属同士を粉砕と圧接作用の繰り返しによって常温下で合金化する方法です。メカニカルグライディングは、合金に機械的エネルギーを与えることによって、アモルファス化したり、合金粉末の焼結性や反応性を向上させる方法です。
メカノケミストリ―について
メカニカルミリングに類似した言葉で、メカノケミストリーがあります。メカノケミストリーとは、物質に粉砕などの機械的応力を作用させた際の結晶構造の変化によって生じる物理化学的性質の変化を取り扱う学問分野です。
当社機器のご提案
SCミル(湿式粉砕、分散)
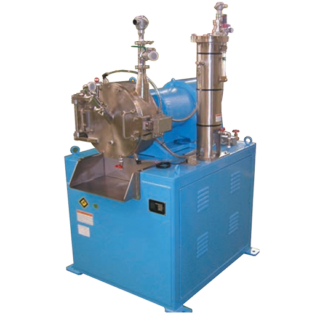
目標粒子径:100~500nm
【クローズドシステム】
湿式プロセスを不活性ガス雰囲気にすることが可能です。待機中の酸素や水分と反応する材料や可燃性のある金属粉末の粉砕もお任せください。
【ポンプレス運転】
ポンプを使わない循環運転が可能です。プロセスラインの洗浄時間の短縮やメンテナンス費用を削減できます。
*大型機や処理物の特性によってはポンプ循環が必要になる場合がございます。
【樹脂・セラミックス仕様】
金属コンタミを低減した粉砕を提案いたします。
MSCミル(湿式粉砕、分散)
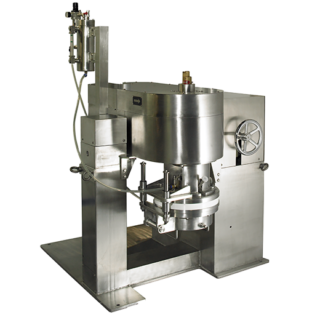
目標粒子径:100nm以下
【クローズドシステム】
湿式プロセスを不活性ガス雰囲気にすることが可能です。待機中の酸素や水分と反応する材料や可燃性のある金属粉末の粉砕もお任せください。
【樹脂・セラミックス仕様】
金属コンタミを低減した粉砕を提案いたします。
アトライタ(湿式粉砕、乾式粉砕、分散)
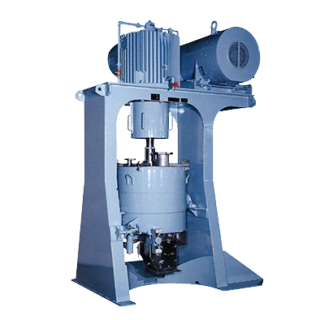
目標粒子径:0.5~500μm(湿式)、5~50μm(乾式)
【耐汚染対策】
接液部を耐汚染仕様にできます。ジルコニア、アルミナ、樹脂などの材質が選択できます。
【クローズドシステム】
真空ポンプを用いてガス置換を行い、低露点下での粉砕が可能です。
【メカニカルミリング】
強力な攪拌力で、メカニカルミリングによるメカノケミカル反応が可能です。
コンポジ(複合化、球形化)
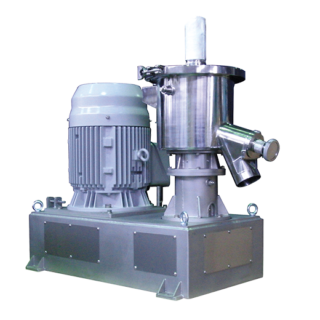
【高速処理による複合化・球形化】
100m/sの羽根周速度と衝突板の効果で従来にない強力なせん断が得られます。効率の良い複合化・球形化処理を実現します!
【スケールアップもお任せ!】
大型機の実績とテスト機を完備し、大型機へのスケールアップを確実に行います!
ダイナミックミル(乾式粉砕)
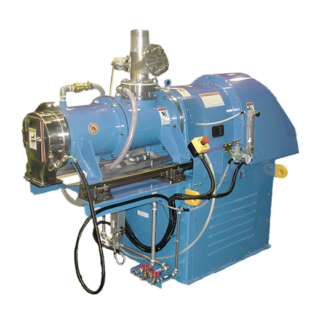
目標粒子径:3~10μm
【クローズドシステム】
プロセスを不活性ガス雰囲気にすることが可能。
【セラミックス仕様】
金属コンタミレスな粉砕をご提案します。
【メカニカルミリング】
金属などの重い材料でも効率良く、偏り無く処理できます。
アルケミ(乾式粉砕)
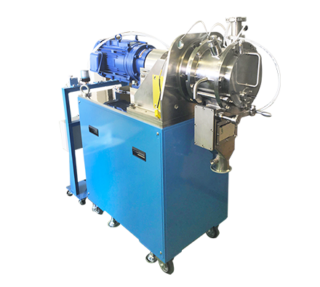
目標粒子径:5~50μm
【クローズドシステム】
プロセスを不活性ガス雰囲気にすることが可能です。
【結晶子サイズの微細化】
微細化による電池サイクル性の向上、伝導性の向上が見込まれます。
【メカニカルミルング】
金属などの重い材料でも効率良く、偏り無く処理できます。
FMミキサ(混合、分散、複合化)
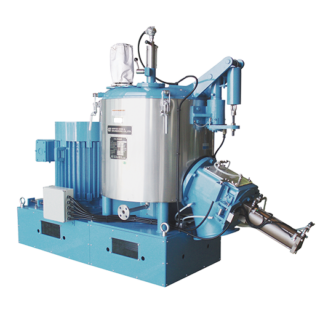
【多種多様な粉体処理】
粉体の均一混合や、高速回転による処理物の複合化も可能。スケールアップにも対応しています。
【耐摩耗処理】
耐摩耗溶射により金属コンタミを低減した粉体処理をご提案いたします。
プラネタリミキサ(混合、混練、分散)
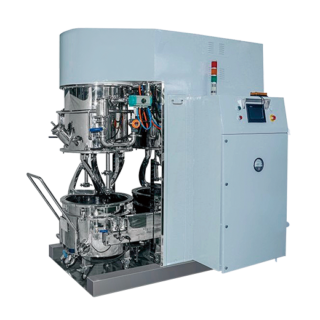
【スラリー化】
活物質のスラリ化および高分散処理が可能です。
【高粘度処理物でも対応可能】
多軸攪拌羽根(2本)とディスパーを設置し、幅広い粘度に対応します。
引用/参考
1)国立研究開発法人産業技術総合研究所
https://www.aist.go.jp/aist_j/press_release/pr2021/pr20211120/pr20211120.html
2)J.Y.Huang, Y.K.Wu and H.Q.Ye: Microsc. Res. Technol., 40 (1998)101
3)電池の情報サイト https://kenkou888.com/
機器導入に関してのご相談から専門的な技術セミナーまで
様々なシチュエーションに対応します。
技術情報には掲載していない情報もお伝えすることができますので、
当社機器にご興味を持たれた方は是非お問い合わせください。